Most common reasons given for accidents at workplaces by employers as well as workers and their unions is Carelessness of the worker involved.
The worker was rushing and did not follow due process
The worker did not use protective equipment
The worker was distracted
The worker acted over-confident
We have heard this and more. Let us now take a step back and think: WHY?
The most common reason for workers to rush and not follow due process is high production targets. Workers are continuously skipping safety protocols to achieve production targets. Targets are not set by workers. It is set by management and enforced by shopfloor supervisors. If workers are not able to achieve the targets, they are disciplined and at times even verbally or physically abused. Fear of this disciplining, makes workers skip safety protocols and not use protective equipment which slows down production. Further, in case of protective equipment, in most cases in the global south the personal protective equipment that is provided to workers does not satisfy the requirement for the work process. For example,
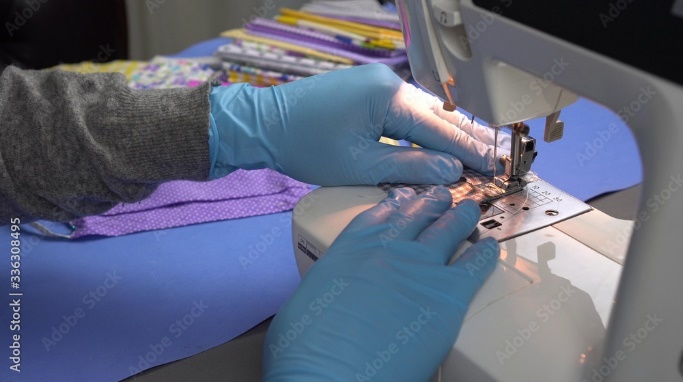
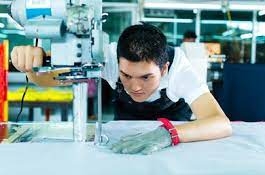
Most garment workers in South Asia are provided rubber surgical gloves (as in figure on the left) for stitching, and that too usually when there is an audit. These cannot protect the workers fingers if they get caught under the needle, while they cause hands to sweat leading to higher possibility of hands slipping. Workers thus avoid using these gloves to ensure both their safety and productivity. The gloves that need to be provided for a worker using a sewing machine is a metal mesh glove (as in figure on the right) that is strong enough to protect fingers from being punched by the needle and also allows the hand to breathe. Thus, on many occasions, the protective equipment provided is not appropriate and hence workers avoid using it. This creates a work culture of allowing hazardous work on the shopfloor. The workers are not responsible for that too. It is the management that allows this to continue to ensure higher production and higher profits.
When workers get used to working daily under hazardous conditions over years for at least 8 hours x 60 minutes x 60 seconds, it creates an illusion that they are skilled enough to not hurt themselves. Most days they do not get seriously hurt or injured. But is it humanly possible for any person, especially one performing repetitive tasks, to keep their attention at 100% for 28,800 seconds in a day and every day? Obviously No. That is when accidents happen and in most cases the worker is held responsible for being distracted. Exhaustion and monotony that results in these kind of accidents is not taken into account. The worker is blamed while it is the organization of work that is responsible for such accidents. Work is organized by the management, now even digitally through different ERP software, to maximize efficiency and productivity. In planning work organization, the management focuses on efficiency and productivity and not on factors that affect humans, such as extreme temperatures, humidity, noise, violence and harassment at work, delivering that efficiency and productivity. Standardised norms lead to increased work intensity and mental stress among workers. This also leads to accidents in many cases.
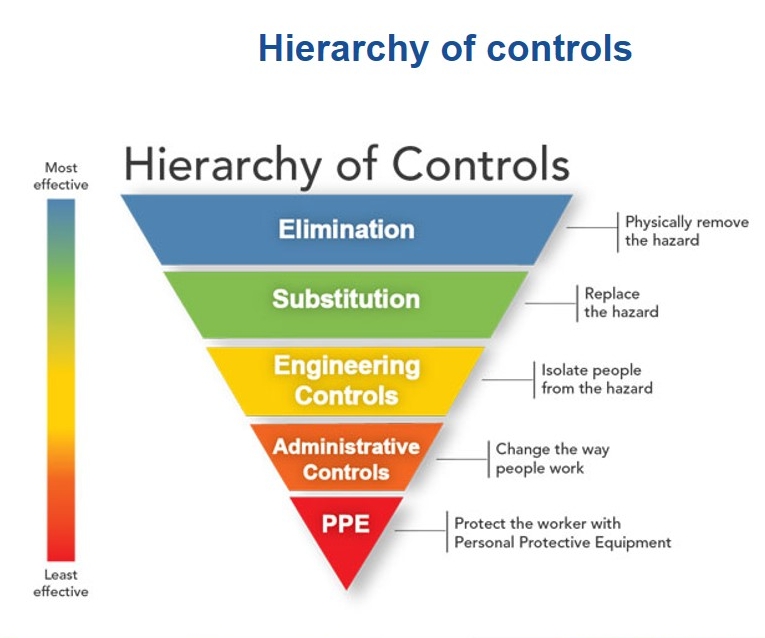
Work organization thus should include mechanisms that prevent accidents. If a certain task or work process is hazardous, employers must first try to Eliminate (physically remove) the hazard – e.g. not use toxic material such as asbestos. If that is an integral part of the production and cannot be eliminated, employers should try to Substitute (replace) the hazard by using alternate chemicals that may be less toxic. If that is also not a viable choice given the nature of the production, management needs to intervene and put in place engineering and administrative controls that change how people work and are exposed to the hazard by rotating workers to reduce prolonged exposure, or creating barriers between the hazard and the worker such as guard rails, etc. But all these cost more money than providing Personal Protective Equipment to workers and hence at best employers choose to do so. In the hierarchy of controls at a workplace to avoid workplace accidents, Personal Protective Equipment is the least effective. However, much of union struggles today are focused on ensuring workers’ access to Personal Protective Equipment. There is a need to re-value life in the global south. If the value of life of a worker in the global south would be equal to that of a worker in the global north, the priorities for ensuring a safe and healthy workplace would also change.
Leave a Reply